Stainless Steel Fabricating Processes
June 15, 2023
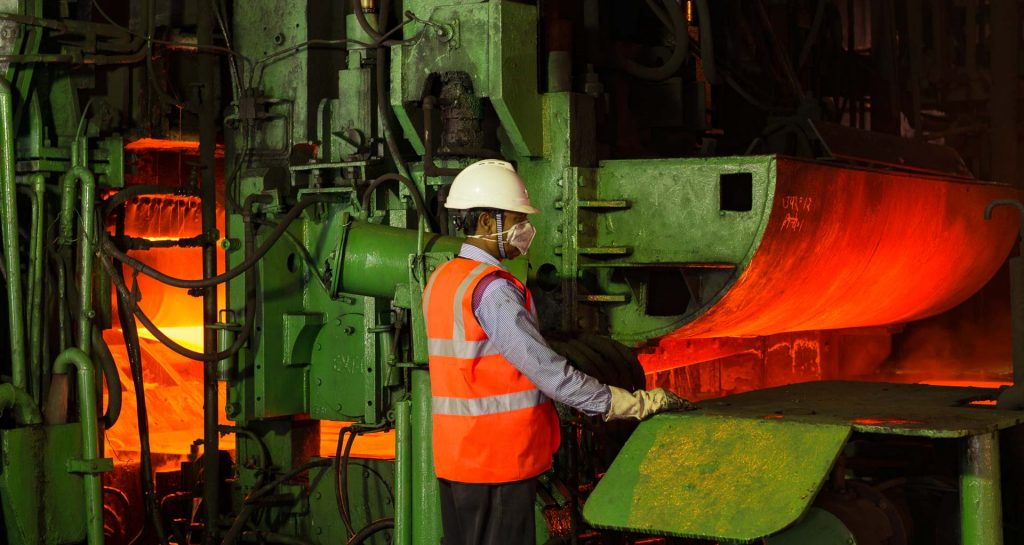
Stainless Steel was accidentally invented by Harry Brearley in 1913 in Sheffield, UK. Since then, every industry recognised the potential of stainless steel, and it flourished in the market. The secret to the success of stainless steel lies in its incredible physical and chemical properties. Stainless steel has high corrosion resistance, heat resistance (up to 1200°C), formability and weldability, durability, and does not rust. On top of this, the metal does not readily react to many substances and is inexpensive compared to specialist, non-corrosive alloys.
How is Stainless Steel fabricated?
The process of making stainless steel includes melting steel scrap, solid casting, heat treating, cleaning, and polishing.
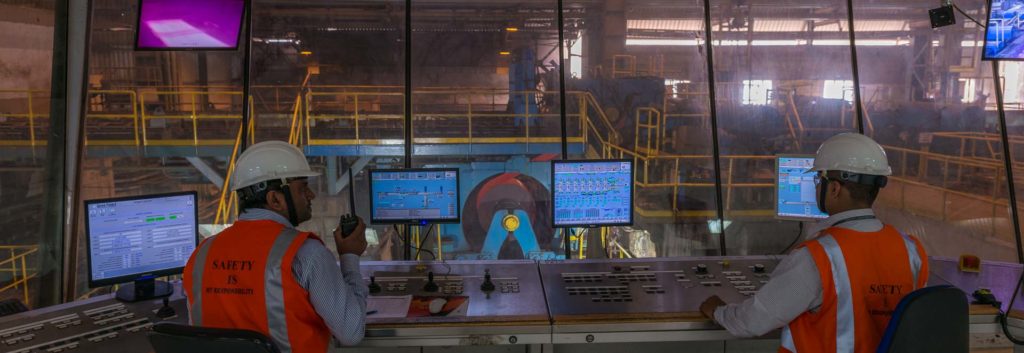
- Collecting the raw materials: Stainless steel is a 100% recyclable material, which means half of the raw material consists of stainless steel scrap with iron, nickel, and chromium. Chromium is essential for the production of stainless steel as there’s no viable alternative. Chromium is a hard, corrosion-resistant transition element that gives stainless steel its corrosion resistance. In general, the higher the chromium content, the more corrosion-resistant the steel.
- Melting the Raw Materials: The different stainless steel materials are placed in an Electric Arc Furnace (EAF) where electrodes heat the mix to its melting point. This process can take anywhere between 8 and 12 hours.
- Removal of Excess Carbon: The mix is then treated in Argon Oxygen Decarburization (AOD) Convertor where pipes blast Argon and Oxygen gases into it. The AOD minimises undesired oxidation and removes excess carbon from the mix.
- Vacuum Oxygen Decarburization: The mix is then treated in a tank degassing unit which is additionally equipped with an oxygen-blowing lance. Due to reduced carbon monoxide partial pressure under vacuum conditions, this process helps in reducing the carbon content of high alloyed stainless steel grades.
- Continues Casting: As the stainless steel begins to cool, it is put through a variety of forming processes-starting with hot rolling while the steel is still above its crystallization temperature. Then the stainless steel mix is cast into stainless steel slabs and stainless steel blooms through a process called continuous casting.
- Grinding: The stainless steel slabs/blooms go through a grinding process to remove any surface defect that has occurred during casting.
- Reheating: The stainless steel slabs are then reheated due to which a rusty scale (oxide) is accumulated on the surface. This scale is removed from the surface by high-pressure water jets in a process called Descaling. The de-scaled metal is finished off with a high-pressure water rinse, leaving a bright, shiny finish.
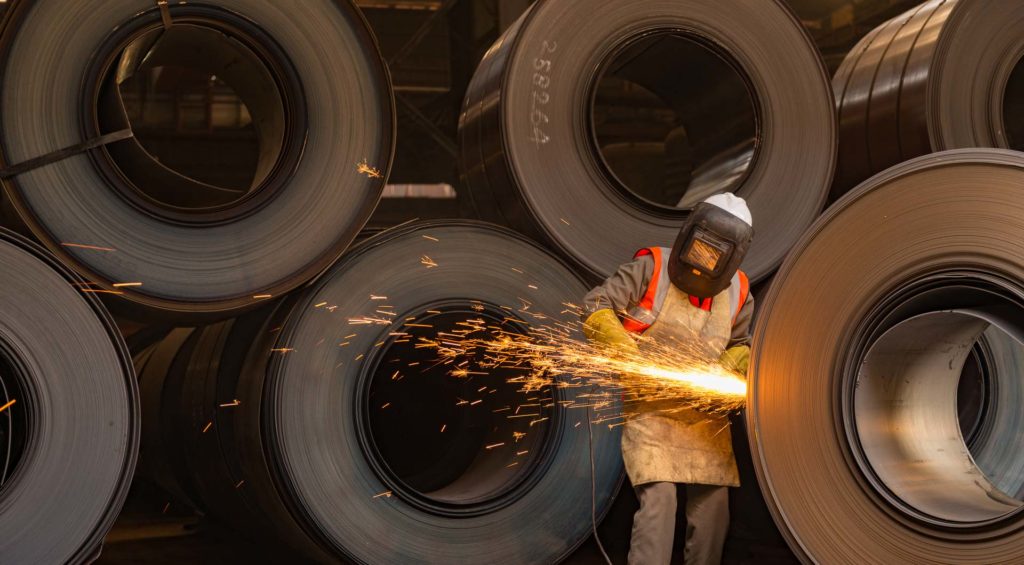
- Roughing and Finishing Mill: The stainless steel slab is then sent back and forth through the Roughing Mill to reduce its thickness and increase its length, without changing its width.
Having acquired the shape of a sheet, it is sent to further thinning in the Finishing Mill, depending on the customer’s requirement.
- Coiling: Then the stainless steel slabs are turned into plates of 20 mm thickness or coils of 6 mm thickness as per order after several intermediate processes.
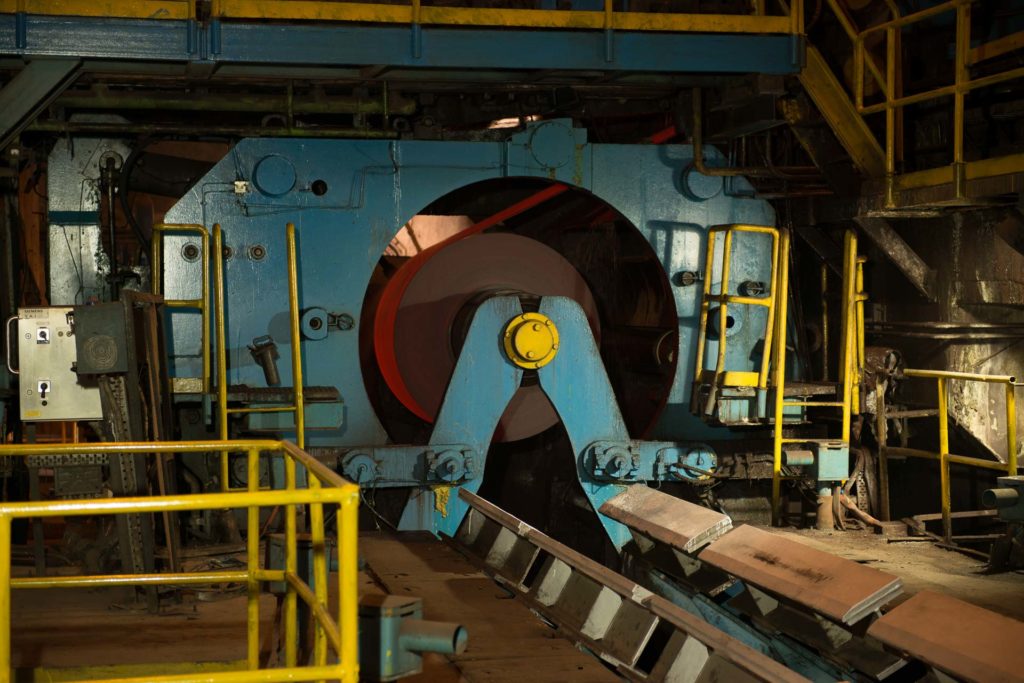
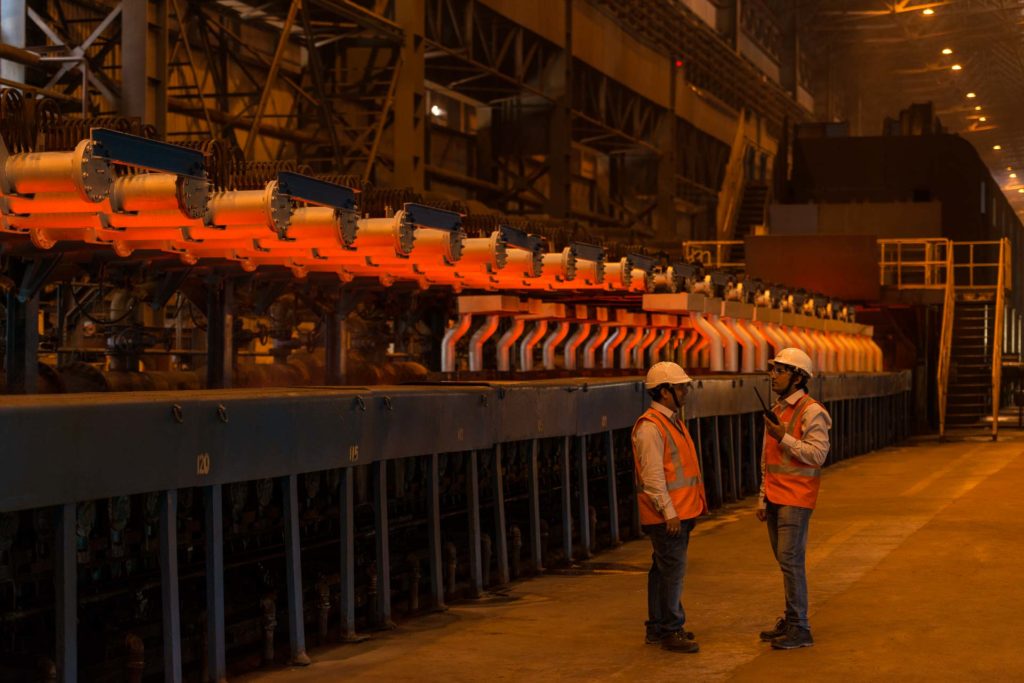
- Annealing: The Hot Rolled coils undergo a thermal process called annealing, in which the metal is given a consistent, uniform internal structure and homogeneous properties. This helps to improve the mechanical stability and corrosion resistance of the coil.
- Quality Testing: There is quality testing at each stage of production, where a sample is taken from the product, and sent to labs for physical and chemical examination. Each gram of stainless steel is planned to perfection.
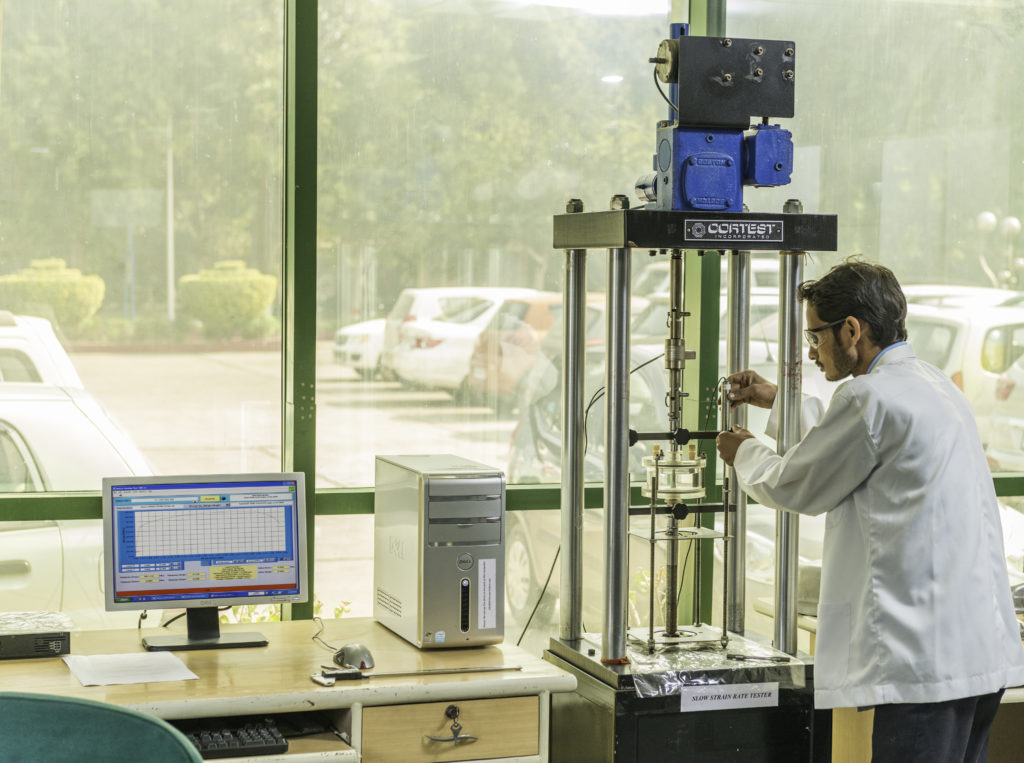
The stainless steel is then customised to HRAP, CRAP, or speciality products like coin blanks and precision strips. This is the stainless steel fabrication process, which makes the magical alloy available to different industries.