Embracing new technology is inevitable for sustainable operations
January 19, 2021
In an interaction with Industry Outlook magazine (December 2020), Director, Jindal Stainless (Hisar) Limited, Mr Jagmohan Sood shares his views on the current trends in the stainless steel industry and the role of new technology adoption in its evolution.
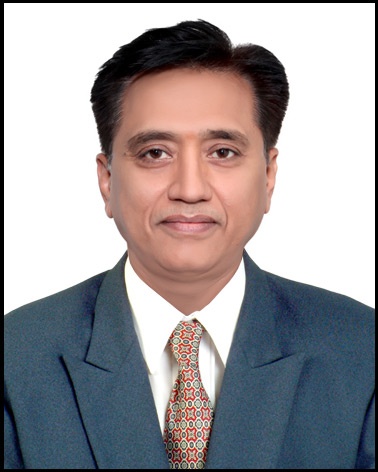
1. India emerged as the second largest crude producer of stainless steel. How do you see the current stainless steel industry in India? What are the major factors driving its growth?
Stainless steel production and consumption in India have been on a growth trajectory; total production reaching 3.92 MMT (million metric tonnes) in CY2019. With a per capita consumption of 2.5 kg in 2019, against 1.2 kg in 2010, Indian stainless steel consumption registered an increase of over 100% in a period of just eight years. This growth has been fueled by the transformation of the Indian infrastructural landscape in the last three decades, with stainless steel increasingly being adopted for modern public applications. The metal’s demand in India has been accelerating in various segments in both B2B and B2C spaces, with Automotive, Railways Transport (ART) and Architecture, Building, Construction (ABC) segments, including process industries like oil & gas, playing key roles. The government’s consistent emphasis on optimizing Life Cycle Cost (LCC) for infrastructural applications has paved the way for all major projects in railway and metros to embrace stainless steel. The government has initiated upgradation and modernization of railway infrastructure, particularly with use of stainless steel in developing foot-over and rail-over bridges and station infrastructure, along with under-frames for railway coaches. Usage of stainless steel in the automobile sector is also increasing due to recently introduced BSVI (Bharat Stage VI) compliance. Despite the pandemic-induced plummet in demand in the first quarter, we are witnessing a V-Shaped recovery, with further improvement in domestic stainless steel consumption on the cards.
2. What are the major challenges in new technology adoption in the steel industry? How can those challenges be addressed?
Indian steel manufacturers stand at varied points across the spectrum of industry’s digital transformation. A few firms are already deploying AI (artificial intelligence) for production gains and minimizing losses, while others are exploring opportunities to upgrade business intelligence using AI and analytics. The steel sector is already amid challenges when it comes to technological transformation. These challenges have now been exacerbated because of the pandemic. Some of them are:
High Capex: The steel industry is highly capital intensive. This limits free cash flow allocation for investments in new or unproven technologies. Hence, the switching time from one technology to another is challenging. Since, initial costs associated with any new technology are high, capital is a major deterrence for initiating technology transition projects.
Trained Workforce: Limited availability of trained workforce for applying any new technology necessitates high expenditure on training of resources, with limited output at times, thereby making it challenging.
Infrastructure: Various companies (especially the smaller steel companies) have relatively old infrastructure, which make any modification difficult to implement and manage.
Despite the above mentioned challenges, it is evident that embracing new technology is inevitable for sustainable operations. The steel industry needs to address these challenges to further enhance competitiveness and productivity, and add innovative products to their baskets in order to target new markets. The organizations moving towards digitization must understand that it is a journey with long-term benefits. Rapid and smooth deployment of some market-proven tools and initiatives can help companies test the waters and solve existing problems in the short-term and prepare themselves for future large-scale digitization.
3. For most Indian steel makers, managing logistics requirements is arduous, challenging and costly. How do you propose to address this challenge?
Unlike China, Japan or Korea, most of the Indian steel plants are geographically landlocked. This adds to the challenge of managing logistics requirements for most steel plants in India. Transportation through roadways for bulk materials is economically unviable. Railways is therefore preferred by steel makers, with more than 80% of their total logistics requirements being met through the railway network. However, Railways also face serious infrastructure constraints. Overdependence of the Indian Railways on revenue from freight traffic, especially from bulk commodities, is one of them. It is well documented that the freight cost of moving materials through the railways, both raw materials and finished goods, is amplified as passenger traffic is subsidized from freight earnings by the Indian Railways. NITI Aayog estimates a relative cost disadvantage for Indian steelmakers at USD 20–25 per tonne of finished steel.
Several initiatives can be undertaken to improve competitiveness, rationalize costs and ensure faster movement of goods:
- A major thrust on expanding railway connectivity
- Fast tracking the implementation of industrial corridors
- Upgradation of physical infrastructure
- Introduction of an end-of-life vehicle policy, to ensure phasing out of old vehicles from the ecosystem and increasing the speed and reliability of road transportation
- Bringing down the transaction time at ports at par with global standards
4. How do you see the application of predictive analytics in the steel industry? How can it be used to develop various data learning models to estimate the quality of the products?
Data mining and predictive analytics are excellent tools that help in optimizing operations and costs, and lowering the defect ratio. Traditionally, in the steel manufacturing environment, product quality is assessed after final production. If the quality metrics do not meet customer requirements, products are either reworked on or discarded. This excess inventory and re-work creates a bottleneck in the continuous production cycle. This cycle further creates room for forecasting quality metrics of finished products.
This way predictive analytics can be applied to industrial data, collected over years, for developing various data learning models to estimate the quality of the products. Jindal Stainless is using advanced data analytics for efficient plant operations with real-time, data-driven decision-making capabilities. Substantial amount of data from various processes, such as procurement, inventory, supply chain, maintenance, sales and marketing, etc. is being used to derive intelligent outcomes.
To unlock the true potential of data at Jindal Stainless, we are continuously raising awareness regarding data analytics among our leadership, in tandem with up-skilling our employees at large.
5. Which technology do you think has massive potential for the power sector and is yet to be harnessed?
I think energy storage technology is yet to be explored. With climate change under global scrutiny, there has been a shift towards employing renewable energy. India, too, is observing a steady transition from fossil fuels towards renewable energy sources. With an ambitious national target to transform 40% of installed power capacity to renewable sources by 2030, energy storage seems to be the key to unlock the true potential of a brand new power sector.
However, a greater dependence on renewable energy and its higher integration with the grid will not come without its share of problems. The intermittent nature of renewable energy and the limitations on its ability to ramp up and down, based on demand, lead to wastage of significant amount of capacity. To counter this, energy banking has been adopted. However, storage industry is still at a very nascent stage and needs to be harnessed efficiently. The best possible bet for energy storage at this time is Lithium-ion (Li-ion) batteries. Their advantages fall into five broad categories: maintenance, longevity, charging speed, safety, and ease of charging. Though, the Government has already come up with a few measures to promote Lithium-ion battery manufacturing and usage, it needs to initiate a concrete action plan to boost local manufacturing, which would go a long way in making renewable power more lucrative in the future.
6. What are the challenges in implementing an IoT framework within a steel plant to monitor the health and status of the machines? How can they be addressed?
Internet of Things (IoT) is a budding subject in the Indian steel industry, however, there are certain challenges in terms of implementing the IoT framework.
Absence of industry success stories/roadmap
It is hard to trace any players in the industry who have tried and succeeded in such implementations, hence no case studies are available for reference. In addition, several implementation partners present an enticing array of benefits for these big budget projects, but unfortunately, even their own skills and experience in such implementations are inadequate. Thus, the absence of a clear roadmap makes it a risky proposition.
In my view, one of the methods to address this challenge is to look for the similarities in problem statements in other industries like automotive, and take a cue. It will also be beneficial to begin the change with low magnitude projects to control initial costs.
Unavailability of operational data
Historical data of machine health and failures is critical to model and predict patterns indicating future failures in an IoT framework. This becomes a major challenge due to the unavailability of OEM and time series data related to various operational conditions especially beyond 3-4 months. This increases the timeline to reap benefits from such implementations. To address this, steel plants can implement a historian system to store past data for several years.
Differences in machine ages and configurations
A steel plant is usually set up over a period of time resulting in mixed ages of its equipment. Additionally, the equipment with varying system configurations could be procured from multiple vendors. These factors may result in equipment incompatibility with latest technology. Another challenge that comes here is upgrading the existing systems/hardware/machines to the latest versions. This usually becomes impossible because OEMs do not certify these upgrades. This is a very critical challenge for IoT implementation. This requires an understanding of the existing machinery and creating an interface between them and the IoT platform.
Scarcity of sensors for extreme operational environments
Steelmaking is synonymous to extreme environments; high temperatures in blast furnaces, high temperature hot rolled coils, etc. Sensors required to capture parameters of machines involved in these processes are not readily available, probably due to the lack of implementation of such IoT mechanisms in the steel industry. To address this, we usually have to come up with an out-of-box solution with the available resources.
I reiterate the fact that industry must first assess its readiness for such projects and adopt a piecemeal approach for implementation of the IoT framework to reap its benefits.
7. Where do you see the stainless steel industry in the near future? What is the road map ahead for Jindal Stainless?
In terms of demand, the National Steel Policy has envisioned a significant increase in steel and stainless steel consumption in India, and action on the steps outlined in the policy regarding the LCC concept have been initiated by the government. As per the Indian Stainless Steel Development Association, the apex body representing stainless steel industry in India, the metal’s demand is expected to grow in the range of 5-6% for the next couple of years. A huge potential for growth in India is offered by a low per-capita consumption of stainless steel, which stands at ~2.5 kg against the global average of ~6 kg. Consumption of stainless steel will be majorly driven by increased infrastructure spending, a thriving automobile market, and a robust railway sector in India. However, the domestic stainless steel industry is still vulnerable to imports.
In terms of future trends, the growth and sustenance of any industry, including ours, will depend on the technological interventions that it will adopt.Pressure on the industry to reduce its carbon footprint is bound to intensify over a few years down the line. Focus on and investment in R&D will be critical in the steel and stainless steel industry’s quest for green manufacturing. Additionally, companies will work towards securing long-term raw material supplies. As for the customer, demand will shift to further product customization. Above all, companies would look for digital solutions as enablers for enhancing overall operational efficiency. Eventually, Industry 4.0 will become integral to the manufacturing ecosystem.
The introduction of technology into the steel making set-up will change the face of traditional manufacturing. At Jindal Stainless, we have identified IT as a key enabler for our future growth and are constantly leveraging it in our manufacturing set-up. In the metal manufacturing segment, Jindal Stainless was a forerunner in digital transformation in 2017. We overhauled our ERP applications and migrated to the HANA database on Cloud. It enabled business transactions and reports to be 10 to 15 times faster. Later in 2019, we implemented BW/4HANA, one of the world’s fastest data warehousing and reporting systems. This was followed by digitization of several processes like paperless RFQ floating system, digitization of manual inventory operations, PO delivery tracking, vehicle loading process, TAT calculation and freight bill processing. We have also adopted Hybris Commerce, an online auction module, and have empowered our customers with an online platform for all kinds of communications and interactions. Going forward, we believe that technology will be the key differentiator for any industry and we are prepared to embrace these interventions as quickly as possible.