Mr Aman Kumar Mishra
February 8, 2018
There is a valiant glint in his eyes, seeking challenges. No, he is not an adventurer, but a defier who competes with his self. Yet, ‘fighter’ is an understatement for him, because he wins with concord. A winner of ‘Innovation in Stainless’ award, he is a creative enthusiast, blazing a trail of successes.
“We should give ourselves time to introspect what are we best at, and where can we excel, and then apply all our energies towards it.”
Here is a story of a young manager who reveled each rung of the ladder, while climbing all the way up. And today, from the meridian of his professional journey, as he looks back, all he sees is a trail of moments worth sharing. Let’s explore each tread, taking a stroll down his memory lane.
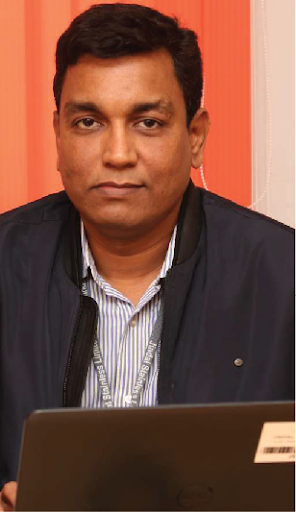
GM-CRM, JSL Jajpur
Tell us about your education and the starting of your professional life?
After completing my mechanical engineering, I got through Indian Institute of Metal, Dhanbad. However, later, I got a seat confirmation in Indore under MP university which then was supposed to be one of the best universities in management studies, and I finally joined the MP university to pursue specialisation in IT and Systems. My propensity towards IT stems from the fact that in 1998, the IT industry was facing a boom, and management students, with a technical eye, wanted to explore careers in IT and I was one of them. Though, as they say sometimes things don’t go as per your plan, because fate has other plans for you and better ones. Amongst plenty of companies that came for recruitment, only one company was from the IT sector. Long story cut short, I couldn’t get placed. Fortunately, I was offered a part-time job with Bharti Televentures, wherein my work was to install VSAT on ATM machines. VSAT is a small satellite aperture used to establish network for ATMs. I started installing this device from one ATM to another, facing the uphill battle, all by myself.
Share your experience of working at Jindal Stainless, Hisar?
I joined Jindal Stainless Hisar as a young 28-year-old Associate Manager, to head the mechanical maintenance of CRD 2 Finishing Lines. On the crest of a wave, I kept on going from success to success in whatever I did. Among my various initial achievements a few are, installation of seam welder at Strip Grinding Line, modification of Skin Pass Mill high pressure hydraulic system, revamping of Strip Grinding Line grinding head No-4, and modification of Strip Grinding Line sludge conveyor system. Also, all the four lines including strip grinding, slitting, skin pass mill and wider BA, were brought in a much better condition after I joined. As a reward for my hard work and sincerity, mechanical maintenance of a newly installed Z-4 Mill was offered to me, which I readily accepted. Not only was the mill stabilized in a record time, but challenging the design and concept of the Original Equipment Manufacturer, also I made many modifications including fixture for Intermediate Roll changing, squeeze roll key, in-house fabrication of POR pull rod, thrust bearing failure analysis, interchangeability of Z-3 and Z-4 mill work rolls, etc. In a brief span of time, the production of the mill reached new heights. Soon after, I was also given the responsibility of Z-3 mill and coil preparation lines. Nothing succeeds like success, thus the story of victory kept going on for me; leaving its trails behind, for me to look back at them and cherish the fruit of my labour.
How did Jajpur happen to you?
Autumn 2010 arrived with new opportunities, and I was offered a role in the team of CRM project at Jajpur. My eagerness to accept this new role overpowered other constraints and I consented for relocation. I finally shifted to the Jajpur plant in December 2010. Initially, I was made responsible for the installation of HAPL line, which was successfully commissioned in 7 months. Soon after, owing to my willingness to seek new roles and positions, I was given a CAPL line too. The breakthrough arrived when I was offered an entirely new role to look after the operations of the CAPL line. I had no prior experience in Operations, yet I accepted it; to quench my ever-augmenting thirst for new challenges. This development in my learning graph ensued ample opportunities, and till date, the line is setting new benchmarks in production day after day. Later, in 2014, I was also given the operations of the CAPL line.
Any interesting memory or incident you would like to share?
In 2014, due to some minor accident the Flying Dye Shear component- a clutch to operate Cut to Length line, broke into several parts. Since this was an imported part, it would have taken three to four months to be sourced from South Korea. Moreover, apart from its own cost which was no less than 60 lakhs, the loss we would have suffered on account of non-production of 1500 mm width sheet, which is produced only in the Jajpur plant, would have been grave. Consequently, I had a random thought to try and make an clutch inhouse. It was certainly a crazy idea, but crazy is what leads to magnanimous outcomes. I gave a fine try, and there we had our very-own, self-made clutch which was compatible enough to run the line. Since then, our indigenous invention is intact and working fine. whereas the clutch that we imported, is lying idle in the store. this along with my other contributions helped me win the ‘Stainless Innovation Award’.
What is your message to the Jindal Stainless family?
I would first like to thank Mr Khulbe and Mr Deepak Aggarwal for entrusting me with freedom to do the work I wanted, without ever doubting my capabilities. Mr Aggarwal, being my reporting manager, has always delegated his responsibility, but never accountability, because of which, I could come this far. I would also like to say that we should give ourselves time to introspect what we are best at, and where we can excel, and then apply all our energies towards it. We should then align it with our individual and organisational goals, and with time, it will spread its spark all around you, to outshine your virtues and make you stainless.