3 Common Methods for Welding Stainless Steel
January 20, 2025
Welding of stainless steel (SS) is essential for many industries, from construction to automotive and aerospace. However, welding of stainless steel presents unique challenges due to its material properties, such as its high chromium content. This content helps prevent corrosion and makes the material more sensitive to heat. The correct stainless steel welding method is crucial to avoid warping, cracking, or contamination. Understanding how to weld stainless steel effectively is key to achieving reliable and long-lasting results.
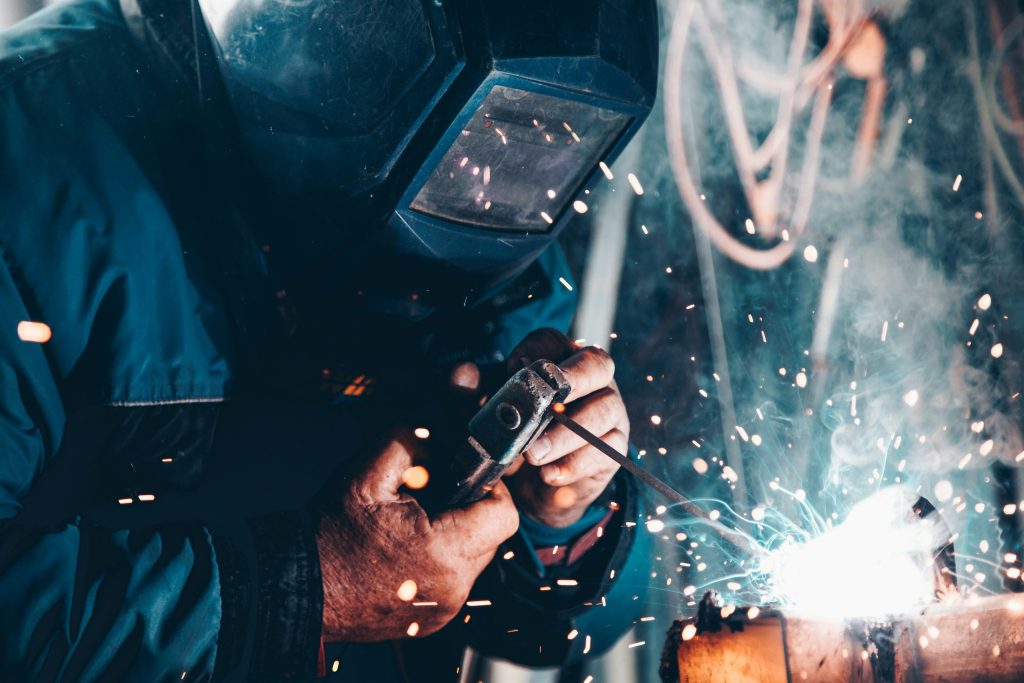
Understanding the Basics of SS Welding
SS welding, or welding stainless steel, requires special attention to heat management and cleanliness. Stainless steel contains at least 10.5% chromium. Three primary classes based on crystal structure: Austenitic (e.g., 304, 316). Ferritic (e.g., 409, 430), Martensitic (e.g., 410, 416) & Duplex (e.g. 2101 & 2205). The “L” grades (e.g., 304L, 316L) denote reduced carbon content. These low-carbon grades are preferred for welding since they could minimise the formation of Cr-carbides near the weld-heat affected zone, thus reducing the “Sensitization” effect. Unlike other metals, stainless steel retains heat more effectively, which can lead to deformation if not handled properly. Proper welding methods for stainless steel focus on temperature control to prevent overheating and warping. Additionally, contaminants like dirt or grease can compromise the weld, so ensuring a clean working environment is essential. SS welding stands out because of its corrosion resistance, but the techniques used differ from those applied to other metals, emphasising the need for precision.
Method 1: TIG Welding (GTAW)
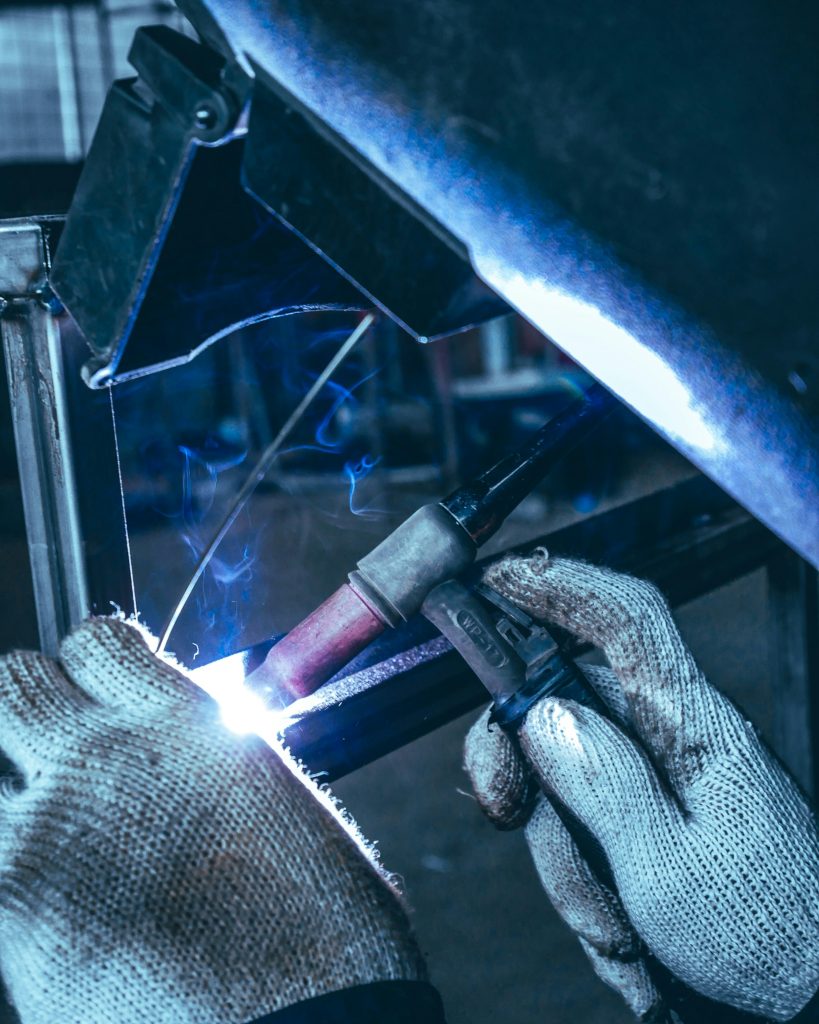
TIG welding, or Gas Tungsten Arc Welding (GTAW), is one of the most commonly used stainless steel welding methods. This process uses a tungsten electrode to create the weld and an inert gas like argon to protect the weld from contamination. TIG welding is renowned for its precision and ability to produce clean, high-quality welds, making it the suitable welding method for stainless steel when aesthetics and accuracy are required. This process is especially suitable for thin materials where detailed work is necessary.
Advantages of TIG Welding for Stainless Steel
TIG welding offers several benefits for welding stainless steel. This method provides excellent control over the heat input, which helps maintain the material’s structural integrity. Moreover, TIG welding ensures that the welded area remains corrosion-resistant, an essential characteristic of stainless steel.
Method 2: MIG Welding (GMAW)
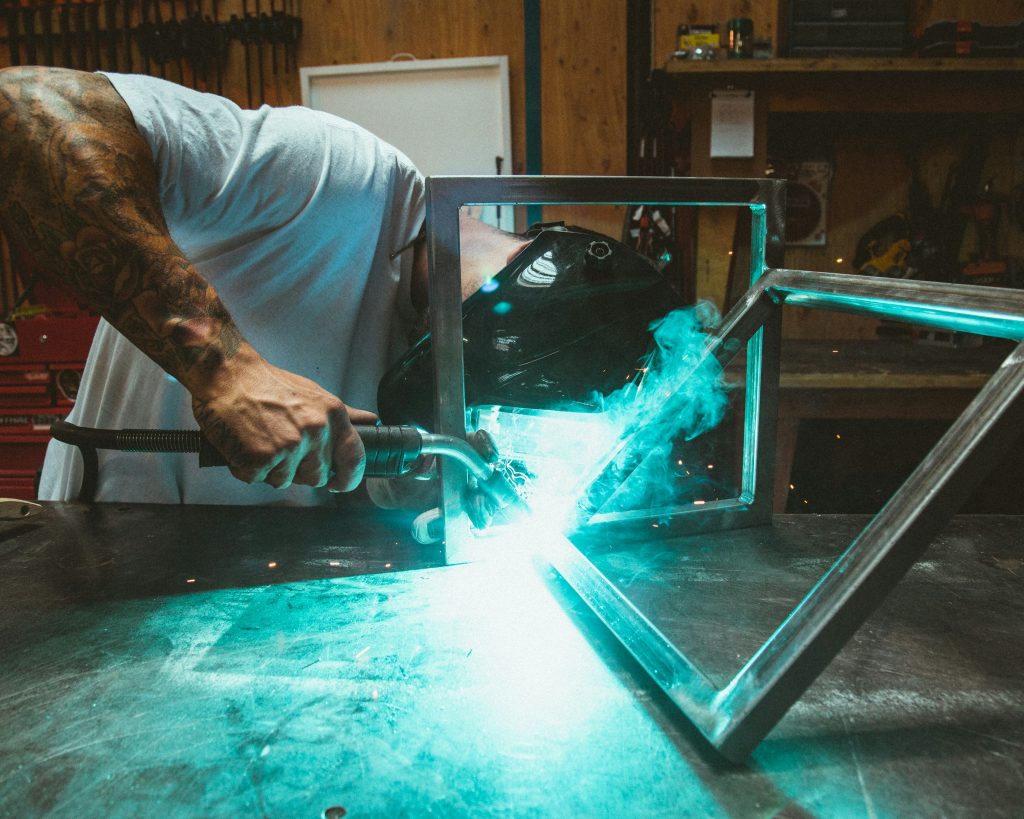
MIG welding, or Gas Metal Arc Welding (GMAW), is another popular stainless steel welding method. This technique is typically used for thicker materials and larger-scale projects. MIG welding uses a continuously fed wire electrode that melts to form the weld, making it faster than TIG welding. It is particularly useful when high productivity is needed without sacrificing the strength of the weld.
MIG welding is considered one of the easier welding methods to master and is widely used in industries where speed and durability are key. Although it may not offer the same level of precision as TIG welding, it is effective for structural applications where aesthetics are less of a concern.
Advantages of MIG Welding for Stainless Steel
MIG welding is ideal for large-scale projects where efficiency is paramount. Its ability to handle thicker materials quickly makes it a go-to stainless steel welding method for construction and automotive manufacturing industries. It is also one of the most accessible types of stainless steel welding, making it a great choice for welders seeking fast results.
Method 3: Stick Welding (SMAW)
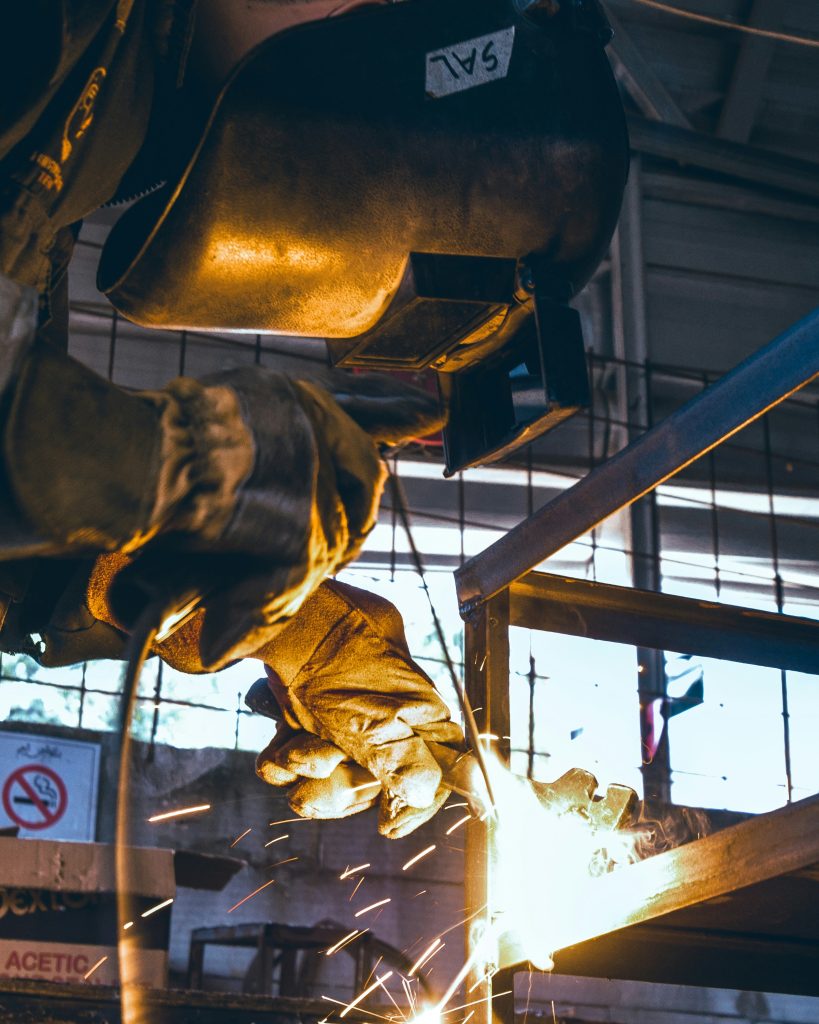
Stick welding, also known as Shielded Metal Arc Welding (SMAW), is a versatile stainless steel welding method particularly suited for outdoor environments. This method uses a consumable electrode coated in flux, which shields to protect the weld from contaminants. Stick welding is highly portable, making it a preferred choice for on-site repairs or outdoor welding tasks.
This method is often employed in industries where environmental conditions, such as wind or dust, make other welding methods impractical. Stick welding is effective for creating durable welds in less-than-ideal conditions.
Advantages of Stick Welding for Stainless Steel
Stick welding’s portability and flexibility make it a valuable technique in environments where other types of stainless steel welding may not be feasible. It is an ideal choice for field repairs and outdoor projects. Because of its versatility, Stick welding is a solid option for industries requiring quick and durable fixes.
Method 4: Laser Welding
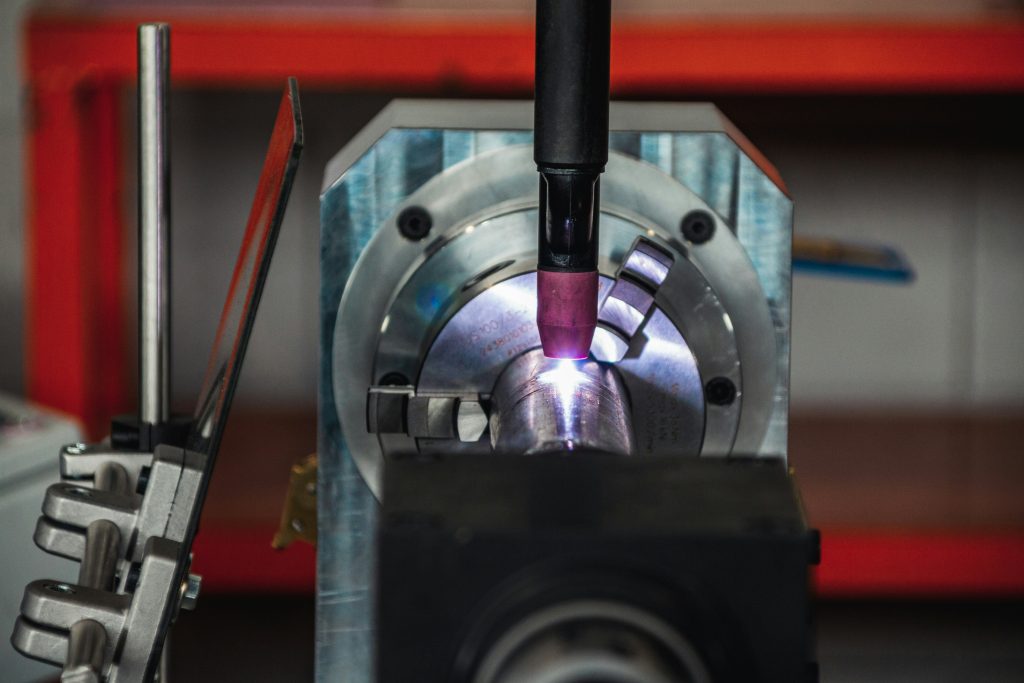
Laser welding is an advanced stainless steel welding method that uses a high-intensity laser beam to join materials. This method is exact and can create immaculate welds with minimal distortion. Laser welding is ideal for intricate or delicate applications, such as medical or electronics industries, where precision and aesthetics are crucial. It’s also suitable for thin and thick materials, offering flexibility across various projects.
Advantages of Laser Welding for Stainless Steel
Laser welding offers several key advantages for welding stainless steel. Its high precision allows for minimal heat input, reducing the risk of warping or distorting the material. Additionally, the speed of the process improves productivity without compromising quality. Laser welding also produces clean, spatter-free welds, making it an excellent choice for industries requiring aesthetically pleasing results. This method stands out for its ability to create strong, reliable joints in even the most demanding applications.
How to Choose the Right Welding Method for Stainless Steel

Selecting the right stainless steel welding method depends on several factors, including the thickness of the material, the project’s quality requirements, and environmental conditions. TIG welding is considered as a good option for stainless steel when precision and appearance are top priorities.
MIG welding is a faster alternative, perfect for larger projects that require sturdy, efficient welds. Stick welding, however, is ideal for fieldwork and repairs, where flexibility and durability are crucial.
When considering how to weld stainless steel, it is essential to evaluate the project’s specific needs. Each method offers unique advantages, and understanding which one best aligns with the project’s goals will ensure long-lasting and high-quality results.
Here is the comparison:
Feature | GMAW (Gas Metal Arc Welding) | GTAW (Gas Tungsten Arc Welding) | SMAW (Shielded Metal Arc Welding) |
---|---|---|---|
Heat Source | An electric arc between a consumable wire electrode and the base metal | An electric arc between a non-consumable tungsten electrode and the base metal | An electric arc between a coated metal electrode and the base metal |
Electrode Type | Uses a consumable wire electrode | Uses a non-consumable tungsten electrode | Uses a consumable coated metal electrode |
Shielding Method | External shielding gas (e.g., argon, CO₂, or gas mixtures) | External inert gas (e.g., argon or helium) | Shielding provided by the electrode coating (no gas required) |
Speed of Process | Fast; well-suited for high-production environments | Slower; focused on precision and control | Moderate; versatile but requires more manual input |
Post-Weld Cleanup | Minimal, depending on the spatter and shielding gas used | Little to no cleanup is required | Requires slag removal using a chipping hammer or grinding |
Material Suitability | Suitable for both thin and thick metals | Best for thin and delicate metals | Ideal for thicker metals |
Flexibility in Position | Highly versatile, usable in multiple welding positions | Extremely versatile and precise | Moderately flexible but requires skill for certain positions |
Typical Applications | Fabrication, automotive, shipbuilding, and industrial projects | Aerospace, artistic welding, and precision industries | Construction, maintenance, and repair work |
Equipment Cost | Medium to high; requires a wire feeder and gas supply | High; involves specialized equipment and shielding gas | Low; simple, portable, and cost-effective setup |
Skill Level Needed | Moderate; easier due to automated wire feeding | High; requires precise control and steady technique | Moderate; requires skill to manage electrode length and arc |
Efficiency | Highly efficient with continuous wire feed | Less efficient due to manual filler metal addition | Moderate; electrode stubs reduce efficiency |
But before starting the welding process, it is advisable to go through the following points in order to ensure safer & quality welds:
- Following Safety Guidelines – ensuring proper ventilation and personal protective equipment (PPE). Safety practices, as recommended by AWS D1.6/ 1.6M and OSHA to be followed in order to protect against fumes, gases, and electric shock.
- Selecting Joint Design and preparation– Type of joint (butt, corner, edge, lap, and tee) Other parameters such as material strength, position, thickness and accessibility for welding. Use of fixtures/ support for stability during welding.
- Welding Process – GTAW, GMAW or SMAW as explained in the above content.
- Shielding Gas Type
- Filler Metal Selection – Matching the filler metal to the alloy for similar properties. For dissimilar metals, compatibility and mechanical properties shall be considered. The welding handbook may be referred to for more information.
- Setting Right Parameters – Weld current, voltage, and wire feed speed with respect to the type of welding, material grade and material thickness.
- Maintaining Weld Cleanliness – Ensuring a clean surface to avoid defects prior to welding. Use an SS wire brush; wear gloves to prevent contamination.
- Preheating before Welding – Typically not necessary for austenitic & ferritic grades but may be required for martensitic grades.
- Proper Welding Techniques – maintaining consistent & optimum speed for adequate shielding.
- Post-Weld Cleaning – Refer to welding standards for more information. Slag removal from welds using chipping or grinding is necessary. Pickling & passivation might be needed in order to improve the surface finish by removing the heat-tint layers.
Conclusion
In conclusion, ss welding offers several methods for different application requirements and project needs. TIG welding is highly regarded as a good option for stainless steel when clean, precise welds are required. MIG welding provides fast, efficient results, making it ideal for large-scale industrial work. Stick welding is a versatile option for outdoor projects and field repairs. Understanding the advantages of each technique will guide you in choosing the right approach for your next SS welding project.