What Is Stainless Steel and How Is It Made?
October 30, 2024
What is stainless steel? It’s a versatile, durable, and rust-resistant alloy that has transformed industries worldwide. Stainless steel is everywhere—from the cutlery in your kitchen to towering skyscrapers. Its unique properties, including corrosion resistance and strength, make it indispensable. But have you ever wondered how stainless steel is made or what metal in stainless steel gives it such impressive qualities?
Understanding its composition and manufacturing process shows why it’s so widely used across industries.
What Is Stainless Steel?
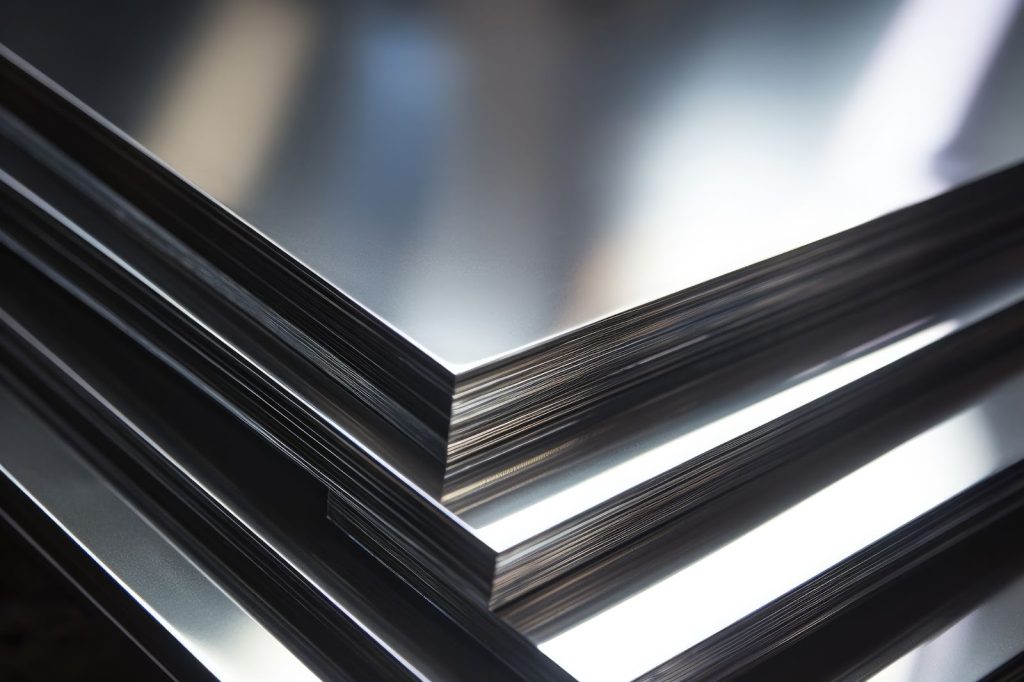
To define what is stainless steel, we must recognize it as an iron-based alloy having chromium additions, primarily known for its corrosion resistance. Its defining feature is its ability to resist rust, making it a reliable choice for environments prone to moisture or chemical exposure.
In addition to corrosion resistance, stainless steel offers strength, heat resistance, and an attractive shine, making it a preferred material for various applications.
So, what is stainless steel made of? It’s more than just iron. This alloy combines iron with other elements, most notably chromium, which is key to its anti-rust properties. Each metal in stainless steel contributes something unique to its overall performance.
What Is Stainless Steel?
When we ask what metals in stainless steel create its unique properties, the answer lies in a blend of different elements.
While Chromium is the show’s star, other metals like nickel, molybdenum, carbon, and even titanium play significant roles in making Stainless Steel an ideal choice for multiple applications.
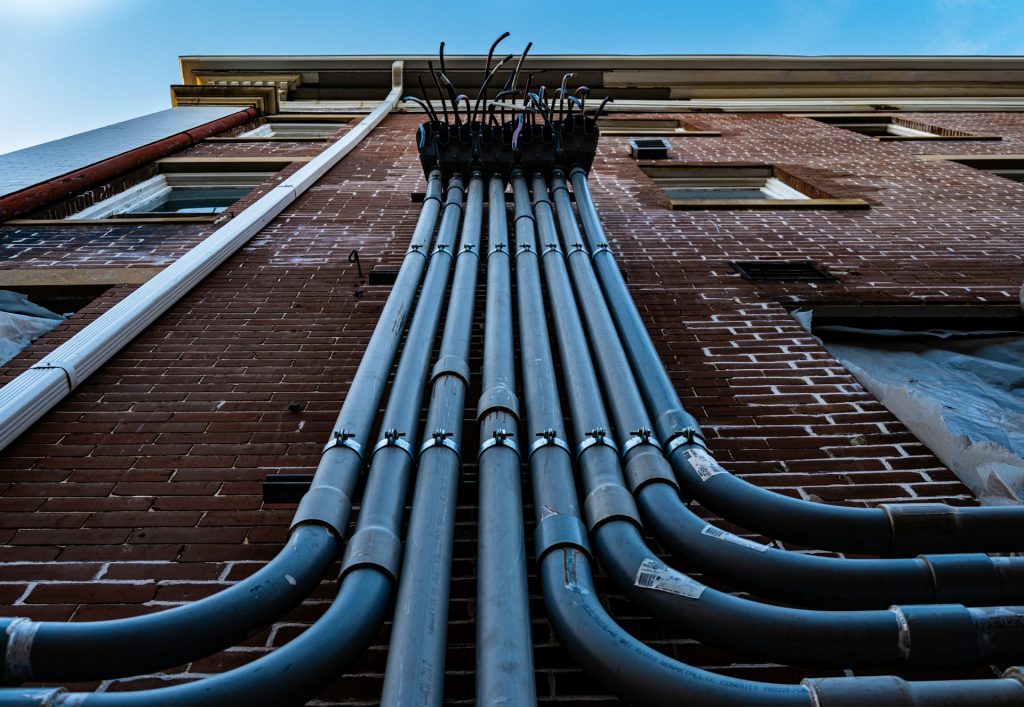
The Role of Chromium
Chromium is an essential metal. Stainless steel must contain at least 10.5% chromium. This element forms a passive layer on the metal’s surface, protecting it from rust and corrosion.
When exposed to oxygen, chromium creates a thin, invisible layer that acts as a shield. This barrier not only blocks out moisture and air, preventing rust but also self-heals if the metal is scratched or damaged.
Other Metals in Stainless Steel
In addition to chromium, other metals in stainless steel include:
Nickel enhances the steel’s toughness, helping it endure extreme temperatures and making it more flexible. Molybdenum improves corrosion resistance, especially in harsh environments like coastal regions or industries with acidic exposure.
Carbon is found in small quantities. It increases the hardness and strength of the alloy. However, excess carbon can decrease corrosion resistance, so its levels must be carefully controlled.
Each of these metals plays a role in determining the overall durability and flexibility of the alloy. Together, these elements form a robust, long-lasting material. But the question remains: stainless steel made of what metal combinations are used to optimize its performance?
This table represents the stainless steel composition percentage for common types of stainless steel
Iron | 50-72% | Manganese | 0.2-11% |
Chromium | 10.5-27% | Silicon | Upto 1% |
Nickel | 1-28% | Nitrogen | Up to 0.32% |
Molybdenum | 0-5% | Phosphorus | ≤ 0.1% |
Carbon | 0.01-0.55% | Sulfur | ≤ 0.03% |
How Is Stainless Steel Made?
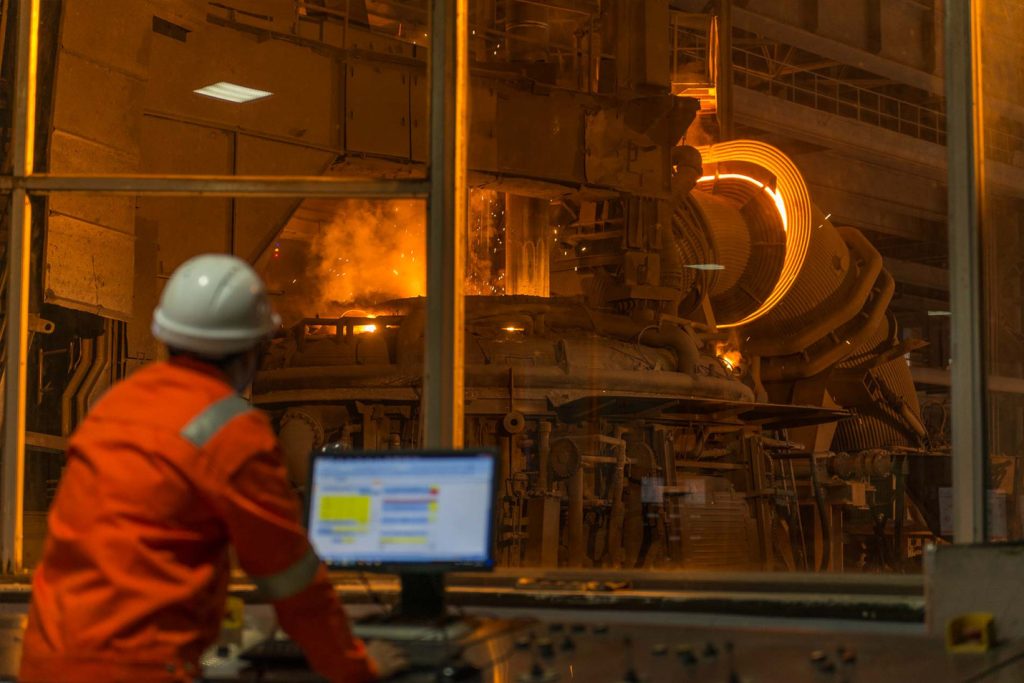
Now that we’ve explored what metal in stainless steel contributes to its properties let’s explore how this unique alloy is made. The manufacturing process includes multiple stages, each vital to achieving the final product.
Raw Materials
The journey begins with the raw materials: iron ore, chromium, nickel, and other alloys like molybdenum. In the case of remelting, suitable stainless steel scrap will be used in place of iron ore. The selection of these materials is essential for determining what metal in stainless steel will dominate the final alloy, dictating its strength and corrosion resistance. These raw materials are meticulously mixed to ensure the alloy’s properties meet industrial standards.
The Melting Process
Once the raw materials are collected, the first step in making stainless steel is melting them in a furnace. This process takes 8 to 12 hours, during which iron ore/ scrap metal, chromium, nickel, and other metals are melted together to form a uniform, molten mixture. The melting & inert gas blowing practices ensure the alloy homogenity. This is the critical point where stainless steel made of what metal truly takes shape
Removal of Impurities
The next step is removing the unnecessary elements in the required chemistry. The process named Decarburisation, involves reducing excess carbon from the mixture. Excessive carbon can diminish stainless steel’s corrosion resistance and formability, so it must be carefully monitored. Similarly, Desulphurization minimizes the sulphur content. Once these impurities are removed, a required composition is said to be achieved, and what metal remains in stainless steel is an ideal mix of iron, chromium, and other required essential elements.
Casting, Hot Forming and Shaping
The molten stainless steel is then cast into blooms/ slabs of required dimensions. And upon solidification after cooling, these cast products are hot-formed and shaped into sheets, rods, bars, or plates, depending on its intended use. Different shaping methods, such as forging, or rolling, help in achieving the desired product profiles. At this stage, stainless steel made of what metal influences whether the final product will be rigid, flexible, or resistant to high heat.
Heat Treatment
Heat treatment is applied to further relieve the internal stresses from the deformed product, thereby enhancing its toughness & ductility, achieve specific grain morphologies. In some cases the strength can be improved by age-hardening treatments. Annealing, one common heat treatment, involves heating the steel and then cooling it slowly. This process relieves internal stresses and improves the alloy’s toughness, on the other hand, quenching practices increase the cooling rates & thereby results in achieving higher strength & hardness at the cost of ductility.
Cold Forming & Finishing
The so formed oxide layer during the Annealing treatments can be removed by Pickling process, which can be then subjected to cold forming processes like cold-rolling in order to achieve the required product dimensions & surface finish. If necessary, in the final stage, the stainless steel is further polished and cleaned as per requirements, resulting in a smooth, shiny surface that is aesthetically appealing and corrosion-resistant. The finishing touches also ensure the steel is prepared for its specific application. Whether it’s cutlery, surgical instruments, or construction materials, what are stainless steel used for depends heavily on how it’s finished.
What Are Stainless Steel Used For?
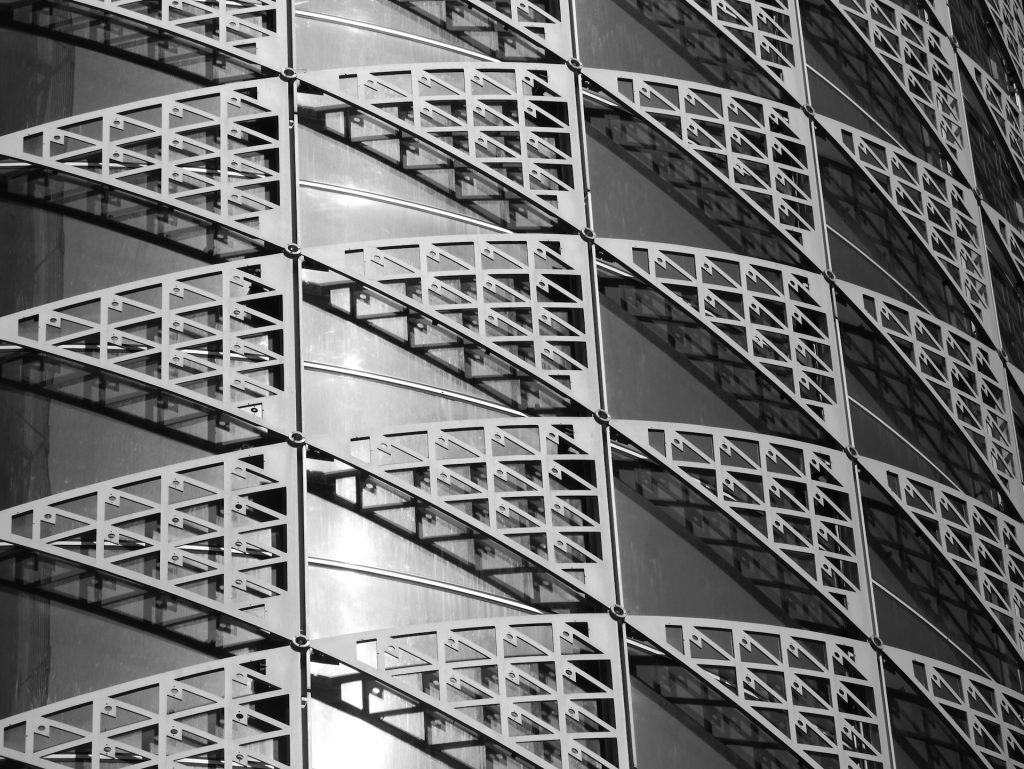
What is stainless steel used for? The answer spans across industries. From household appliances to medical devices and large-scale construction projects, stainless steel is a backbone in various fields. Its resistance to rust and corrosion makes it ideal for applications exposed to moisture or harsh chemicals.
- Stainless steel is used to construct buildings, bridges, and monuments because of its strength and resistance to corrosion.
- It’s the preferred material for surgical instruments and medical devices in healthcare, thanks to its hygienic and non-reactive nature.
- From sinks and faucets to cutlery and kitchen appliances, stainless steel’s durability and aesthetic appeal make it popular in homes.
As we see, what are stainless steel used for can vary, but its advantages make it indispensable for many industries.
Conclusion
Stainless steel is a durable, rust-resistant alloy made primarily of iron, chromium, nickel, and molybdenum. Chromium forms a protective layer, preventing corrosion, while other metals enhance strength and flexibility. It’s produced by melting raw materials, removing impurities, and shaping them into desired product forms like sheets, plates, coils, bars, wires, and rods. Stainless steel is widely used in construction, healthcare, and household items.