Technical Director and A Founding Member, IGP Group, Mr G Ganesan
August 30, 2024
This energetic octogenarian is here to share some wisdom! The Technical Director and Founding Member of IGP Group, Mr G Ganesan, has a message for budding engineers: “Always stay connected with end users during the development process—their feedback can spark valuable updates and drive innovation.”
With over six decades of experience and a dominant market share in India’s gasket manufacturing sector, IGP Group has continually pushed the boundaries, pioneering industrial gaskets that meet both national and international standards. Dive into this engaging conversation between Supriya Sundriyal from Corporate Communications and Mr G Ganesan for a glimpse into IGP’s growth and the evolution of gasket manufacturing market over the years.
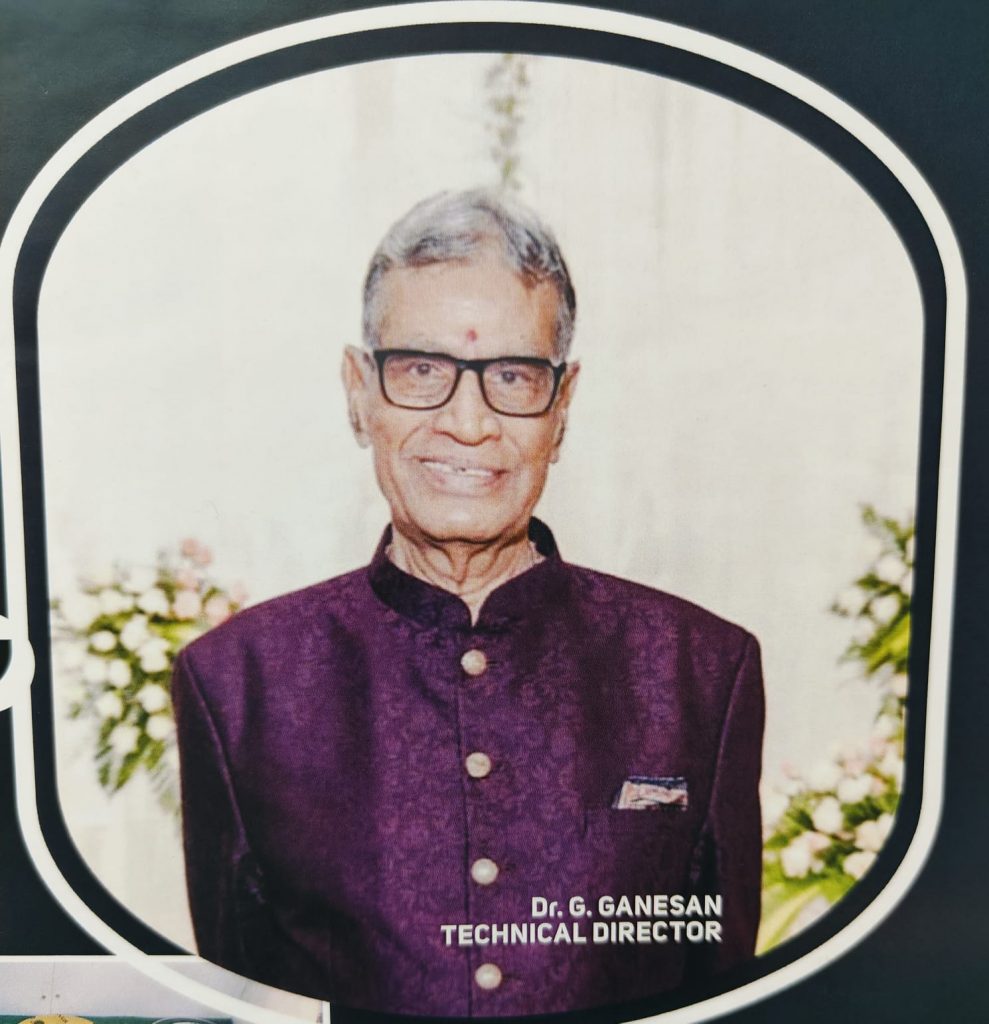
1. Please tell us about yourself and about your company. What are your main products and target markets?
I am the Technical Director and one of a Founding Member of the IGP Group, based in the heart of Chennai. Our IGP Company manufactures and supplies all types of industrial gaskets, serving not only India and also the global market. IGP enjoys major share of the market for Industrial Gaskets manufactured and supplied in India.
Gaskets are essential components that play a crucial role in preventing the flange joint leaks, and ensure safe, secured, and effective and leak free and peaceful performance of the entire installation. They are widely used in various sectors, including melting, mining, refining, oil and gas pipelines, power generations and petrochemical industries, valve manufacturing industries, pressure vessel equipment, heat exchangers and nuclear power plants etc.
As for myself, I hold a degree in Mechanical Engineering from Chennai. Throughout my career, I have been invited by organisations such as the Indian Space Research Organisation (ISRO), the defence sector, petrochemical Industries and Design & Engineering organisation and equipment manufacturers to discuss special needs and challenges to ensure leak free joints and safe assemblies and peaceful operations. While I used to frequently engage with students at universities, my visits have become less frequent due to my age. However, I still enjoy interacting with the next generation whenever possible.
2. How has IGP Group witnessed the evolution of the oil and gas industry? How have the customer demands changed over time?
As far as the power and petrochemical industries are concerned—particularly in oil and gas testing and operations—we have been deeply involved since the industry’s inception in India.
For private sectors like Reliance , L&T, Godrej and others and also public sector companies like IOCL, BPCL, and HPCL , BHEL and others, we have been supplying all types of industrial gaskets as per Indian and international standards and specifications for over 60 years.
We are supplying to them exclusively designed and developed custom-built industrial gaskets.
Initially, these special Industrial gaskets were imported. And we worked closely with the Government of India’s Indigenous Development Committee and also with the reputed national and international Design and Engineering organisations, prominent end users to indigenously develop, manufacture, and supply these special industrial gaskets meeting the international standards and specification. The safety and compatibility of materials, particularly various grade of stainless steel, have always been of utmost importance.
In the early years, India lacked the specific grades of stainless steel required for these applications, which needed to be soft and pliable for effective sealing.
Over a period, the stainless steel industry has improved significantly, and today, Indian manufacturers are capable of producing the required stainless steel with the appropriate hardness levels. The quality standards continue to evolve, enhancing the performance of gaskets and preventing gas leakage and permeability, which are critical for the safety and efficiency of these applications.
3. Does the usage of stainless steel aid in the quality of your products? What makes stainless steel the most suitable material?
For gaskets used in bolted joints, it’s crucial that the stainless steel material is both tough and at the same time yield to capable of penetrating the sealing surface effectively. Therefore, for gasket applications, the material should be sufficiently soft to ensure an easy and free flow of the gasket on the flange contacting face and effective seal of the flange assembly by still maintaining required resilience to recover and retain tightness after compression. Continuous improvement is essential in developing these gaskets, and the evolving requirements demand new types, designs, constructions and materials.
Our team has designed various special types and construction of these gaskets. I have personally visited many sites to ensure our products meet the highest standards. We’ve worked closely with customers and end users from the start to develop gaskets that meet the mechanical and quality requirements of the final product and ultimate usage .Interaction between users, designers, and manufacturers is critical to ensuring the gaskets meet these standards and requirements. Our ongoing commitment to quality has been a key factor in our ability to continuously supply gaskets that meet the evolving needs of the industry, in line with the continuously upgrading Indian and international standards and specification and also to meet the special and specific requirements of the customers and end users.
4. Any specific innovation that IGP has undertaken while manufacturing gaskets?
At the time of erection and installation of many petrochemical plants in our country during 1960s, they faced the critical problem of the imported gaskets getting damaged during transit. We placed to them our interest and initiative to indigenously develop these industrial gaskets and innovate and improve them and serve them safely on time.
We were supported by the Government formed Indigenous Development committee, which included members from many major petrochemical Sectors and Design & Engineering organisations.
With serious, sincere, and united team work we were able to get all the end user requirement as feedback to enable us to successfully develop these special industrial gaskets meeting all national and international standards and quality requirements.
One of the key requirements was the development and production of the spirally wound metallic gasket with resilience, which was essential for maintaining a tight seal. This resilient gasket became crucial for various applications, including some in the nuclear industry. The Technical Development Committee recognised the need for quality and resilience over cost considerations. By interacting with end users and experts, we were able to meet these stringent requirements and successfully develop a product that addressed the industry’s needs.
5. When did your association with Jindal Stainless begin? What sets Jindal Stainless apart?
Our association with Jindal Stainless begin some three decades ago and it has been a wonderful journey with them. This partnership has grown stronger over the years and we are hopeful that it will be further strengthened as the time passes. We hope that Jindal Stainless also continue to innovate and makes more products that cater to our industry.
6. What advice would you give to future engineers who wish to join the industry and make a meaningful impact on society?
I want the future engineers to also focus on the products and its requirements. By thoroughly studying product requirements, you can identify new opportunities for innovation. Also, it’s important to maintain communication with end users during any development process, as their feedback can lead to valuable updates and improvements. Collaborating closely with other engineers and treating engineering as a continuous process, rather than just a task, will enhance both your business capabilities and overall performance.